Exploring Innovations in Laser Welding Machines and Their Impact on the Welding Industry
Jordan Foster • November 14, 2024 • 4 min
The welding industry is witnessing a transformative shift with the advent of advanced laser welding technology. As manufacturers and suppliers continue to innovate, the market for laser welding machines is growing, offering enhanced precision and efficiency.
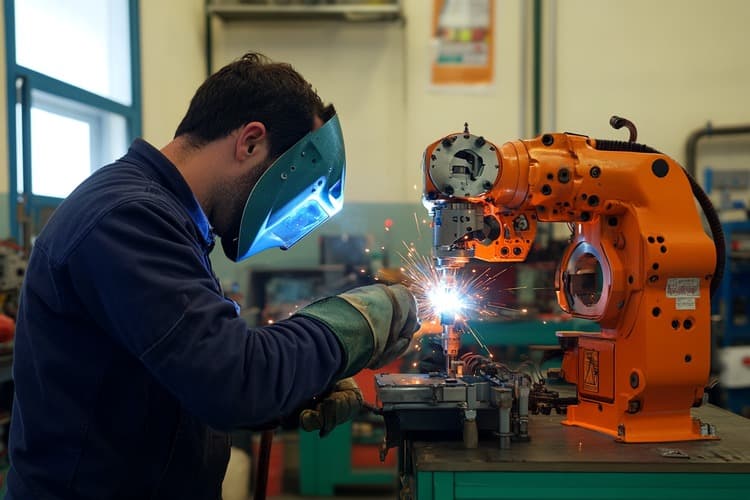
This article delves into the latest trends in automated welding systems, discusses equipment pricing, and reviews the newest solutions shaping industrial welding today.
The Evolution of Laser Welding Technology
Laser welding technology has come a long way since its inception. Initially developed for high-precision applications in the aerospace and automotive industries, it has now found its way into a broader array of industrial uses. The primary advantage of laser welding is its ability to deliver precise and clean welds with minimal heat input, which reduces the risk of material distortion.
Advantages of Laser Welding
-
Precision and Accuracy: Laser beams can be focused on very small areas, allowing for extremely precise welds. This capability is crucial for industries that require high-quality joins, such as electronics and medical device manufacturing.
-
Speed and Efficiency: Laser welding is typically faster than traditional methods, which can significantly boost production rates. The speed and efficiency of laser welding machines are particularly beneficial in high-volume manufacturing settings.
-
Versatility: Laser welding can be applied to a wide range of materials, including metals, plastics, and even dissimilar materials. This versatility opens up new possibilities for innovative product designs and applications.
-
Non-Contact Process: Since laser welding is a non-contact process, there is minimal wear and tear on the equipment, reducing maintenance costs and downtime.
Emerging Trends in Automated Welding Systems
Automation is playing an increasingly pivotal role in the welding industry. Automated laser welding systems are at the forefront of this shift, providing consistent quality and reducing the need for manual intervention. These systems are equipped with advanced sensors and control algorithms that ensure optimal performance and adaptability to various welding tasks.
Integration with Robotics
The integration of robotic arms with laser welding machines has revolutionized the production line. Robotic laser welding systems offer unmatched precision and repeatability, making them ideal for applications that require complex or repetitive welding tasks. These systems are particularly advantageous in automotive manufacturing, where precision and speed are paramount.
Real-Time Monitoring and Quality Control
Modern laser welding machines are equipped with real-time monitoring capabilities. These systems use cameras and sensors to provide instant feedback on the welding process, allowing operators to make adjustments on the fly. This feature not only enhances the quality of the welds but also minimizes material waste and reduces rework costs.
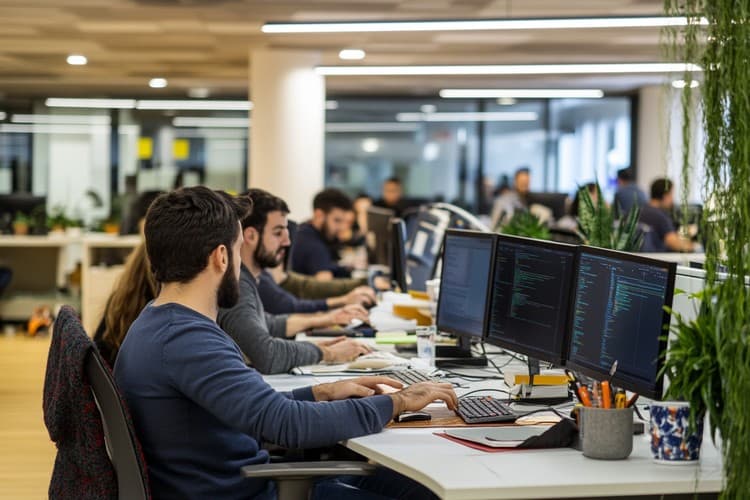
Understanding Laser Machine Pricing
The cost of laser welding machines can vary significantly based on several factors, including power output, automation level, and additional features. Here’s a breakdown of the key considerations that affect laser machine pricing:
Power and Capacity
Higher-powered laser welding machines tend to be more expensive but offer the capability to weld thicker materials and achieve faster speeds. The choice of power level should align with the specific requirements of the application at hand.
Automation Features
Machines with advanced automation features, such as robotic integration and real-time monitoring, command a higher price. However, these features can lead to long-term cost savings by improving efficiency and reducing labor costs.
Customization and Add-Ons
Some manufacturers offer bespoke solutions tailored to specific industrial needs. These customized machines, while more costly upfront, can provide substantial returns on investment by enhancing productivity and reducing downtime.
Reviews and Recommendations of Laser Welding Equipment
With numerous options available, selecting the right laser welding equipment can be daunting. It’s essential to review and compare different models based on factors such as performance, reliability, and support services offered by the suppliers.
Performance and Durability
When reviewing laser welding machines, consider their performance metrics, such as speed, precision, and material compatibility. Additionally, evaluate the durability of the machine components to ensure long-term reliability.
Supplier Support and Services
Reliable welding equipment suppliers offer comprehensive support services, including installation, training, and maintenance. Opting for a supplier with a strong support network can enhance the operational efficiency of the welding equipment.
Conclusion
The innovations in laser welding machines are significantly impacting the welding industry by enhancing precision, efficiency, and versatility. Automated systems integrated with robotics and real-time monitoring are setting new standards in quality and production capabilities. Although initial investments in laser welding equipment can be substantial, the long-term benefits in terms of productivity and cost savings are considerable.
For businesses looking to stay competitive in the rapidly evolving industrial landscape, investing in advanced laser welding technology can be a game-changer. By understanding the nuances of pricing and supplier options, companies can make informed decisions that align with their operational goals and manufacturing needs. As the welding industry continues to advance, embracing these innovations will be key to future success and growth.
Disclaimer: The information provided in this article is for informational purposes only and should not be considered as professional advice. Prices are accurate as of the publish date and may vary over time.